Elegoo Neptune 3 Plus Review
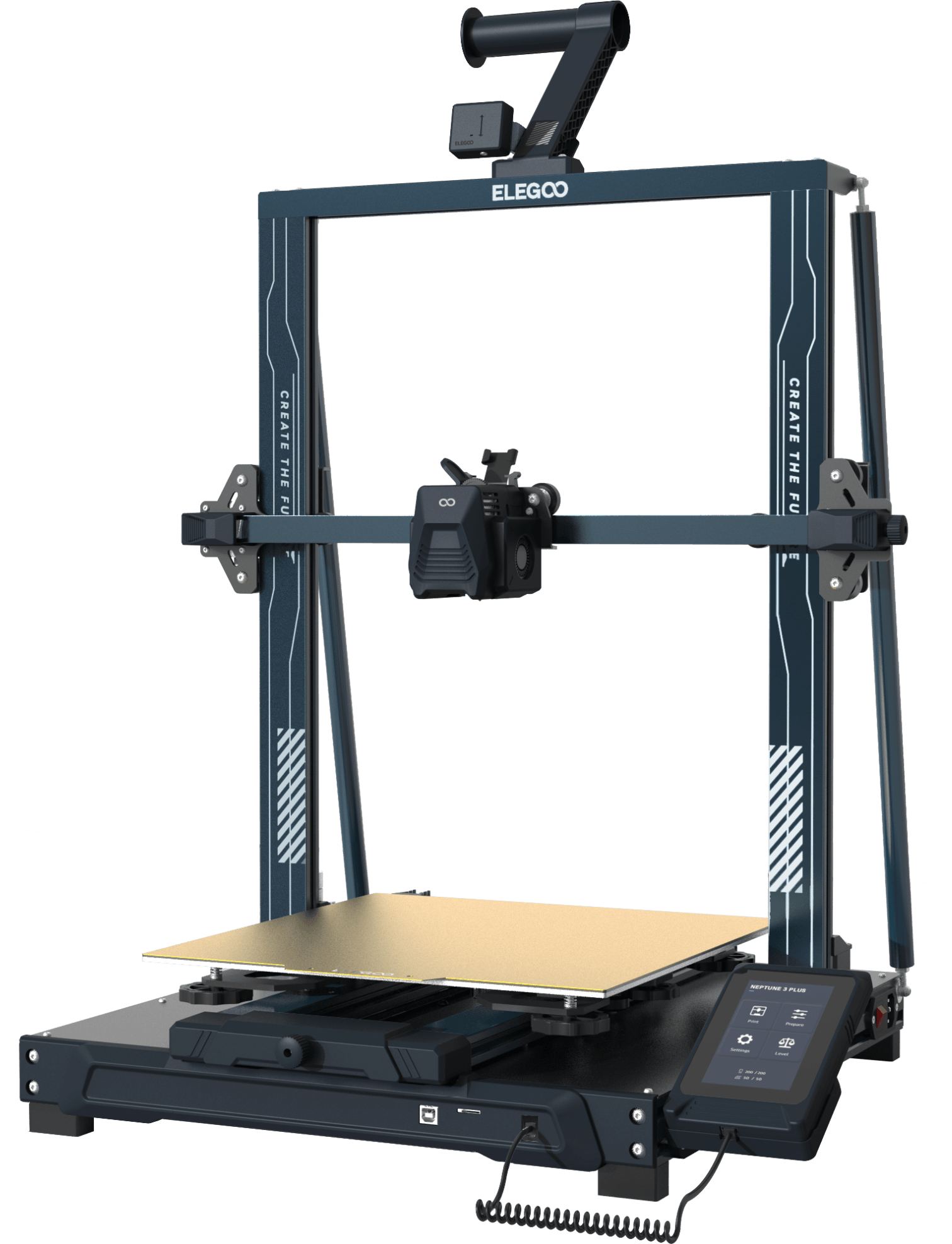
Elegoo Neptune 3 Plus
Built on the feature set established by the Elegoo Neptune 3 Pro, the 'Plus' version brings a larger build volume to the table with many of the features you could want in a desktop 3D FDM printer.
Pros:
- Direct extrusion
- Large, clear and responsive controls
- New integrated LED lighting
- Power Outage Recovery
- 320 x 320 x 400mm build volume
Cons:
- Very tall machine - won't fit under most cabinets
- Front mounted USB port
- Printer head cable management
Where to buy:
- Amazon: Elegoo Neptune 3Plus
- 3D Jake (They have great stock levels): Elegoo Neptune 3 Plus
What is it?
Basically put, the Elegoo Neptune 3 Plus is the larger version of the Neptune 3 Pro FDM 3D printer. If you're not familiar with the 3 Pro then you can read my review for that here. Don't fear though, I will include everything you need to know in this review and probably a few extra superfluous points along the way!
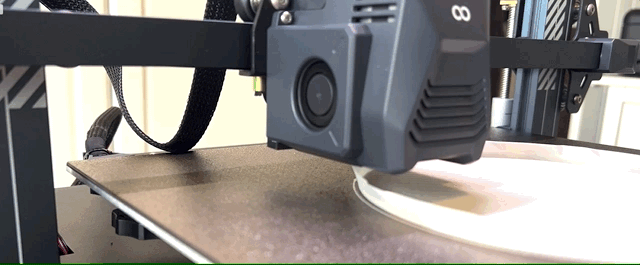
What is an FDM printer?
First up a brief description of a what a FDM printer actually is. FDM (Fused Deposition Modelling) printers have been found in domestic homes far longer than other 3D printing technologies such as resin based MSLA (Masked StereoLithogrAphy). As such their price continues to become more affordable and the technology is proven, refined and easy to work with. I cut my teeth on 3D printing with an FDM printer and mostly use them to this day.
They work by 'slicing' the 3D computer model into thin horizontal slices, usually about 0.15 to 0.2mm high. Each slice is then extruded in molten plastic by the print head which draws one of these 2D slices onto the build platform before raising the nozzle height and proceeding with the next slice. As layer upon layer is laid down on top of the previous layer a 3D object is created. Voila.
The Technical Overview
Printing Technology | FDM | |
---|---|---|
Print Volume | 320 x 320 x 400mm | |
Layer height | 0.1 to 0.4mm | |
Max. nozzle temperature | 260℃ | |
Max. bed temperature | 100℃ | |
Printable Filaments | PLA, ABS, PETG, TPU, TPE and infused (i.e wood, marble etc.) | |
Extrusion Type | Direct Extrusion System |
For a more detailed technical table please see the end of this review.
The printers main selling point is its much larger build volume. Measuring 320 x 320 x 400mm it provides a massive 40,960cm³ of printing room. This is over 254% larger than the Neptune 3 Pro's build volume of 16,065cm³ (its build volume measures 225 x 255 x280mm). This is a substantial print size ability allowing you to print bigger objects in one piece, or many smaller/ standard size items unattended.
The print bed is removable and magnetic. This makes detaching a print super easy and quick, just wait for it to cool then bend the plate slightly - your print will pop right off. The surface on the plate has a slightly textured finish which helps hide the printed lines on the first layer whilst encouraging adhesion when you need it.
The power supply has been integrated inside of the base which makes for a slicker visual appeal and one less item to assemble. On earlier version the PSU fan seemed to run constantly, however on the model I'm testing the PSU fan reduces in volume as its work load decreases. (i.e. after a print has finished and the machine is idle).
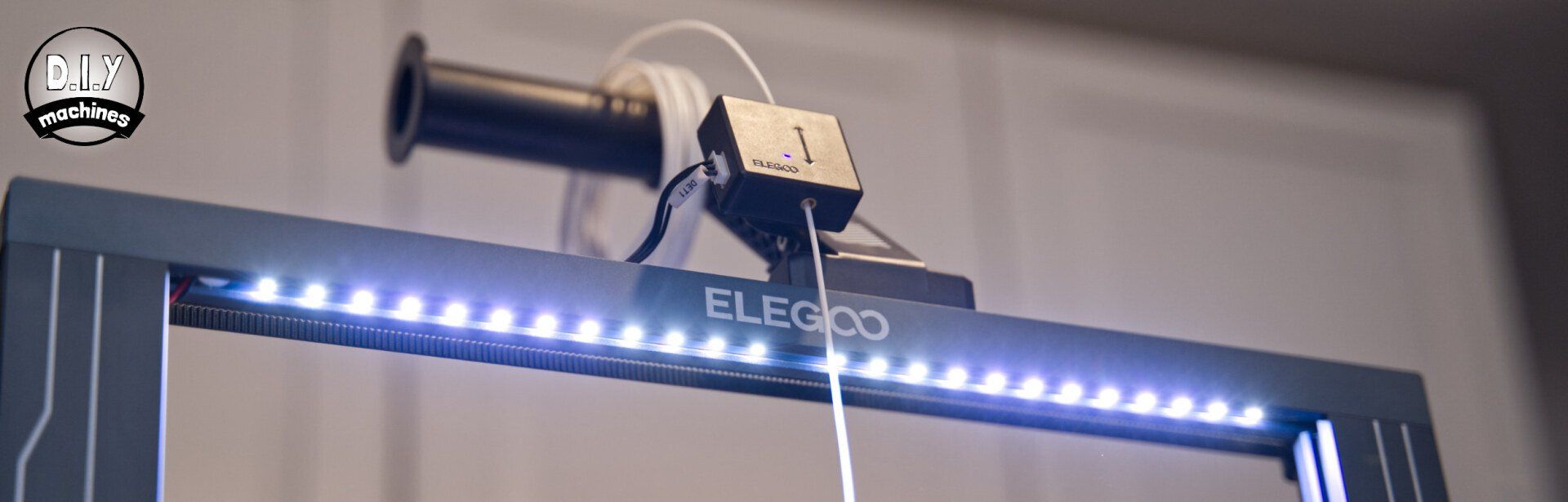
Integrated LED Lighting
As featured for the first time on the 3 Pro, this model also sports integrated LED lights. These are found nestled inside the top gantry. I thought they would be gimmicky - when in fact I'm finding them very useful for illuminating the machine whilst preparing and actually printing the models.
Connectivity
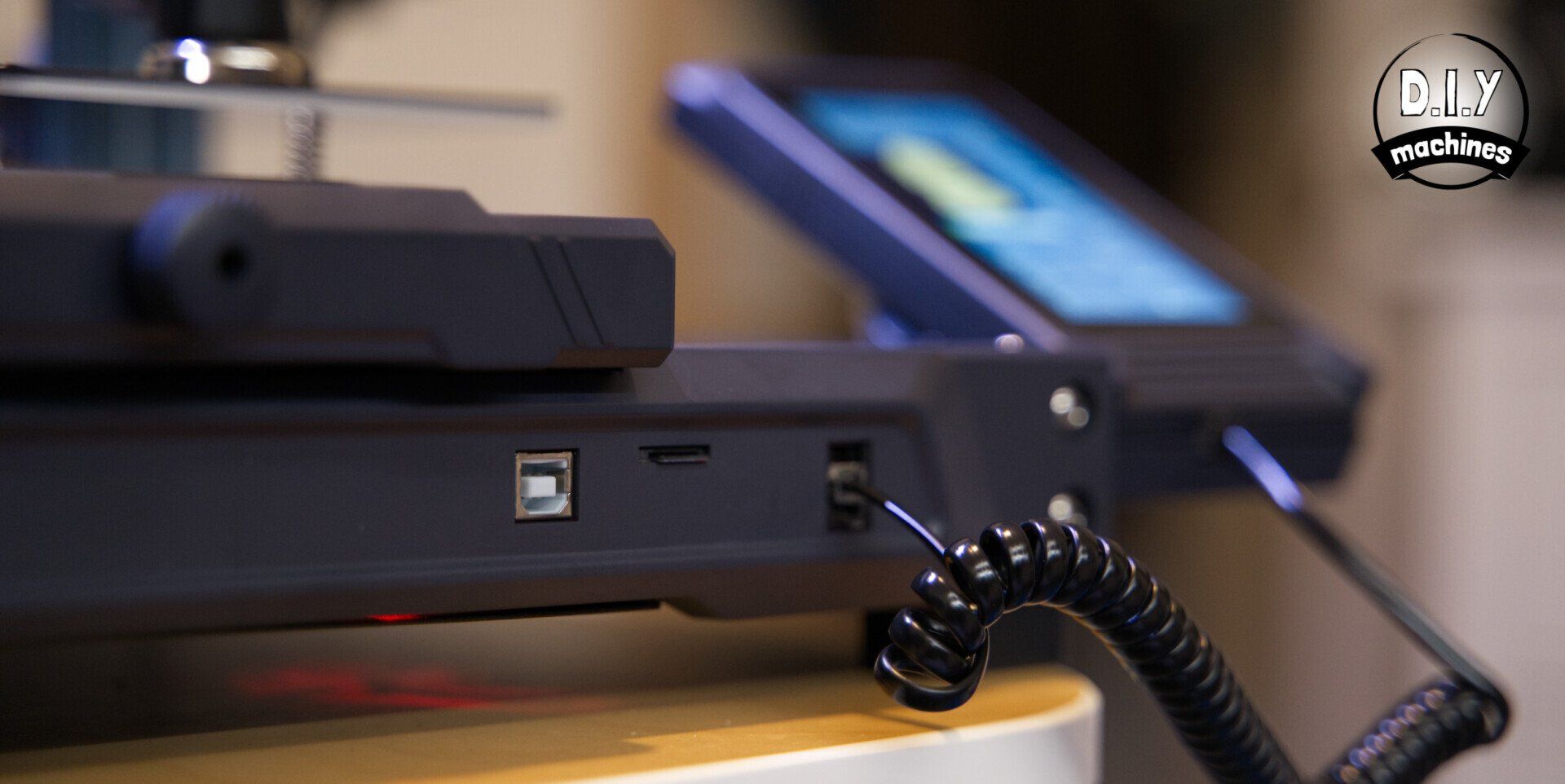
The power switch and kettle lead connections are mounted on the right hand side towards the rear of the machine. The USB and memory card slot is mounted on the front of the machine. I personally think that this a great spot for the memory card slot but I prefer the USB port on the side and failing that the rear. This is because I think it is less prone to damage when the machine is connected to a computer for direct printing. I often set-up a Raspberry Pi running OctoPrint to manage my printers and this manages your printer via USB.
Extruder
The Neptune 3 Plus uses a direct drive extrusion system. This is my preferred method of extrusion over the use of a Bowden Tube.
Pros:
- Increased ability to print with flexible filaments.
- Better print quality through constant extrusion control.
- Faster retraction.
- Simpler extrusion path.
Cons:
- Reduced print speeds because of heavier print head.
- More elaborate print head design required.
Unlike most Direct Drive setups though. Elegoo have kept the filament sensor attached to the frame of the machine instead of the print head.
Having used the same sensor setup on the Neptune 3 Pro for a little while I now prefer this for several reasons; it reduces complexity of the print head, provides the system with earlier warning of filament run-out, and holds the filament strand whilst unloading/loading the print head preventing it from quickly knotting your spool of nicely pre-wound filament if you inadvertently let the end of the spool go.
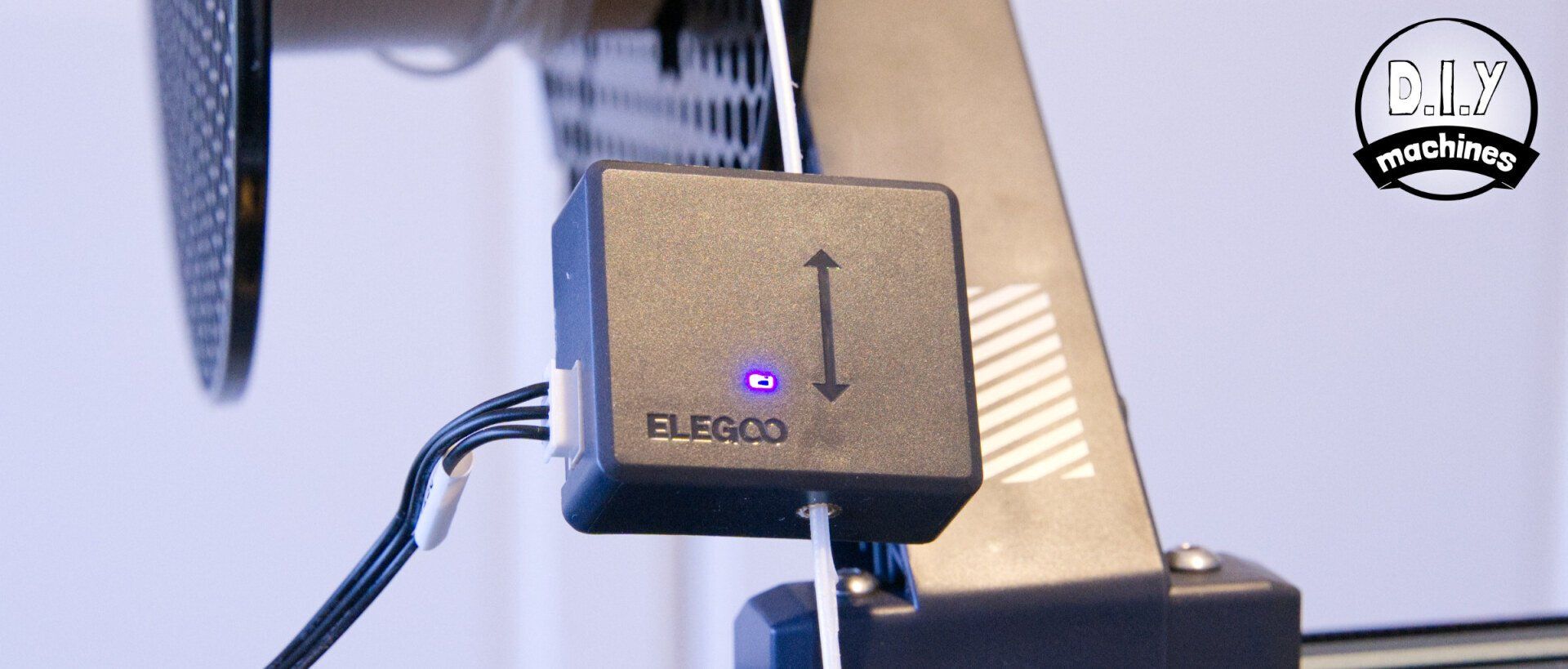
The printer features auto-levelling to compensate for any undulations in the print surface. The printer takes no less than 47 readings across the entire print surface to create a digital map of the surface which it then uses to adjust the printing height as it moves around the platform. Should the compensation required be too drastic there are large knobs placed on the underside of the platform in six locations. (Three along each side). This will allow you to manually remove most of the unevenness before the printer then re-runs its levelling procedure to make final adjustments automatically.
The power outage recovery feature is now becoming common place on any printers. This is certainly welcome on a machine with such a large print volume as it's likely to need to print for days when printing the largest of items. It would be a disaster if a power cut ruined a multiple-day print towards the end.
The power recovery feature will detect power interruptions and offer to re-heat the bed and nozzle before resuming where it was before the power failed. The main drawback of this feature is that it only work when at least 10mm of the print has already been completed - I assume this helps ensure the print it continues with is unlikely to have warped whilst cooling. However, you are still at the mercy of whether the print detached itself from the print bed as the surface cooled - which is what it is designed to do in normal circumstances.
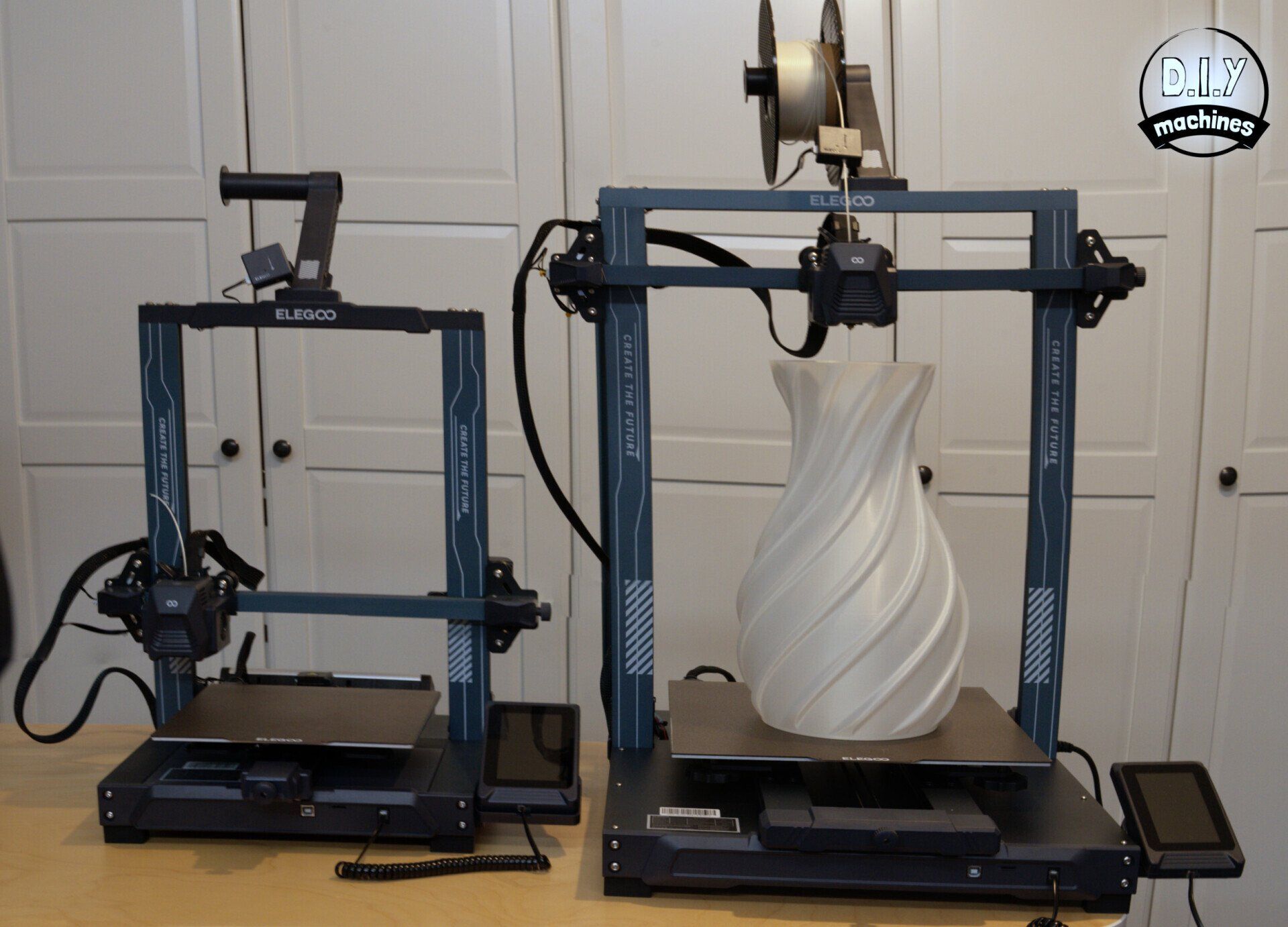
Shipping and Packing
I have had plenty of packages from Elegoo over the years and I'm yet to experience any damage to the products inside. The Neptune 3 Plus arrived with an opening torn in the top of the box which, thanks to the dense foam packing, had no impact on the printer itself.
Being a larger printer the box unsurprisingly larger as well. The shipping box measures 70 x 60 x 25cm (perhaps this is the first bit of superfluous information I mentioned earlier?).
There are not too many individual items inside the box. Everything is well packed and labelled for quick and easy identification. The base of the printer itself is large and carries a reassuring weight. The printing platform decided to extend itself as I lifted it from the packaging which was not super helpful when getting it onto the table. 🤣
What else is included?
There are plenty of accessories included. More than enough to kit you out if this is your first FDM 3D printer, plenty of spare parts and all the tools you would need to repair and maintain your new machine. The parts list is almost identical to the Neptune 3 Pro with the exception of additional bolts to assemble the vertical braces. (Nuts and bolts for assembly are omitted from the below photo).
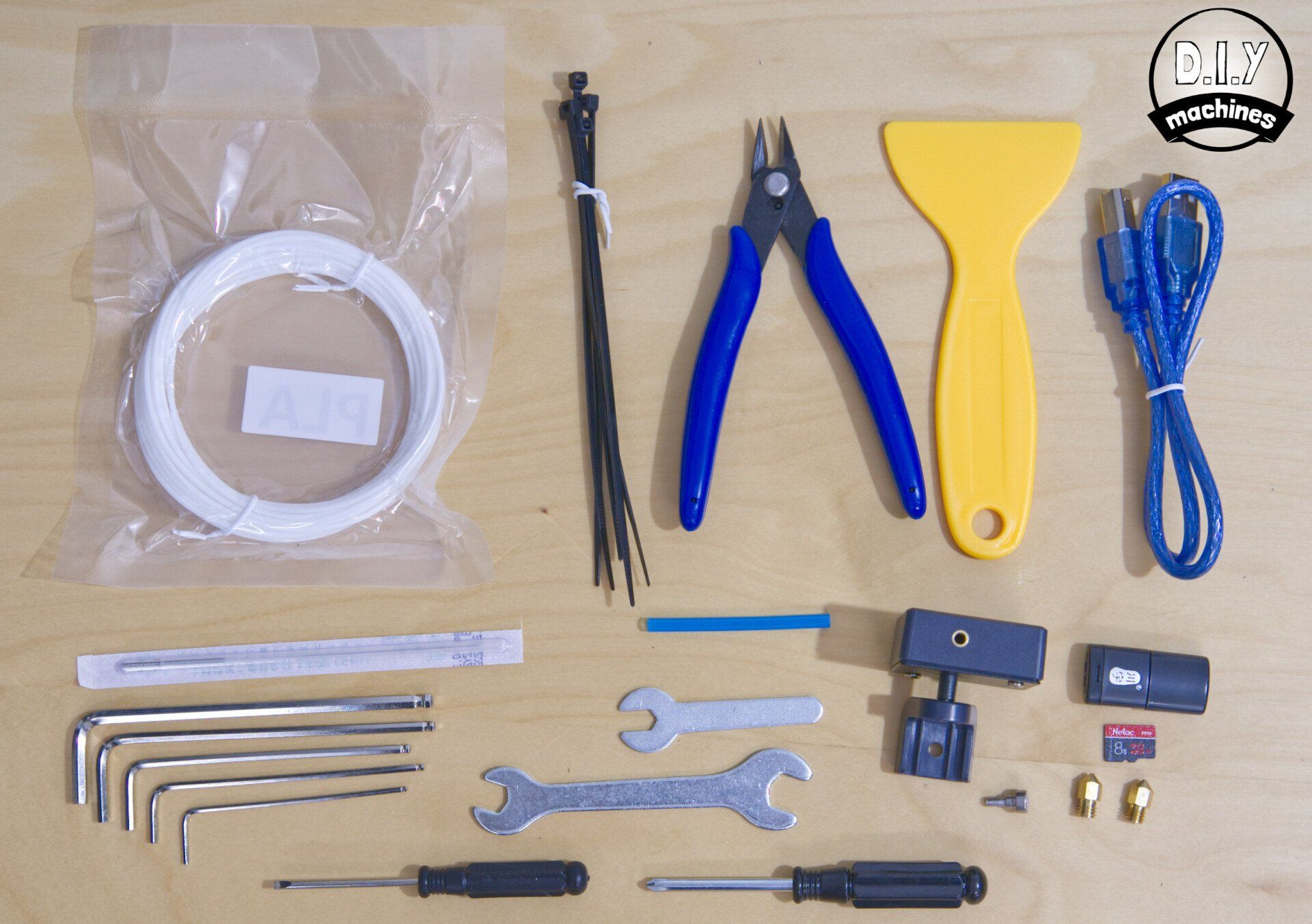
- Print removal spatular
- Spanners for changing nozzle
- Two spare brass nozzles
- Acupuncture Needle (to clear blockages)
- Screwdrivers (Philips and flat head)
- Selection of Allen Keys
- Micro SD / TF Card
- USB Memory Card Reader
- PTFE Tube (Spare)
- Flush Snips / Cutters
- USB Cable
- Sample of PLA Filament
- Cable Ties
- Bolts for assembly
Assembly
This is genuinely so simple it's almost difficult to write about. Essentially the printer arrives in two major halves; the base and the vertical frame. The vertical frame and base are bolted together with four bolts (two each side). This is best done on the machines side. You can then right the printer and attach the control screen (one cable) and it's mount (three bolts). The spool holder and filament sensor are attached with just three more bolts at the top.
As this machine is so tall it includes two bracing rods which run from the back of the machine to the top. Again, four bolts and a couple of washer and they're installed in just seconds.
Electronics
All the wiring for the various motors and sensors have already been thoughtfully routed around the machine and present themselves ready for connection alongside the correct component.
To help ensure the correct cable goes to the correct part each one is labelled and uniquely sized connectors are used. I didn't need to consult the instructions save for ensuring I had not overlooked any. I mean it's almost impossible to make a mistake.
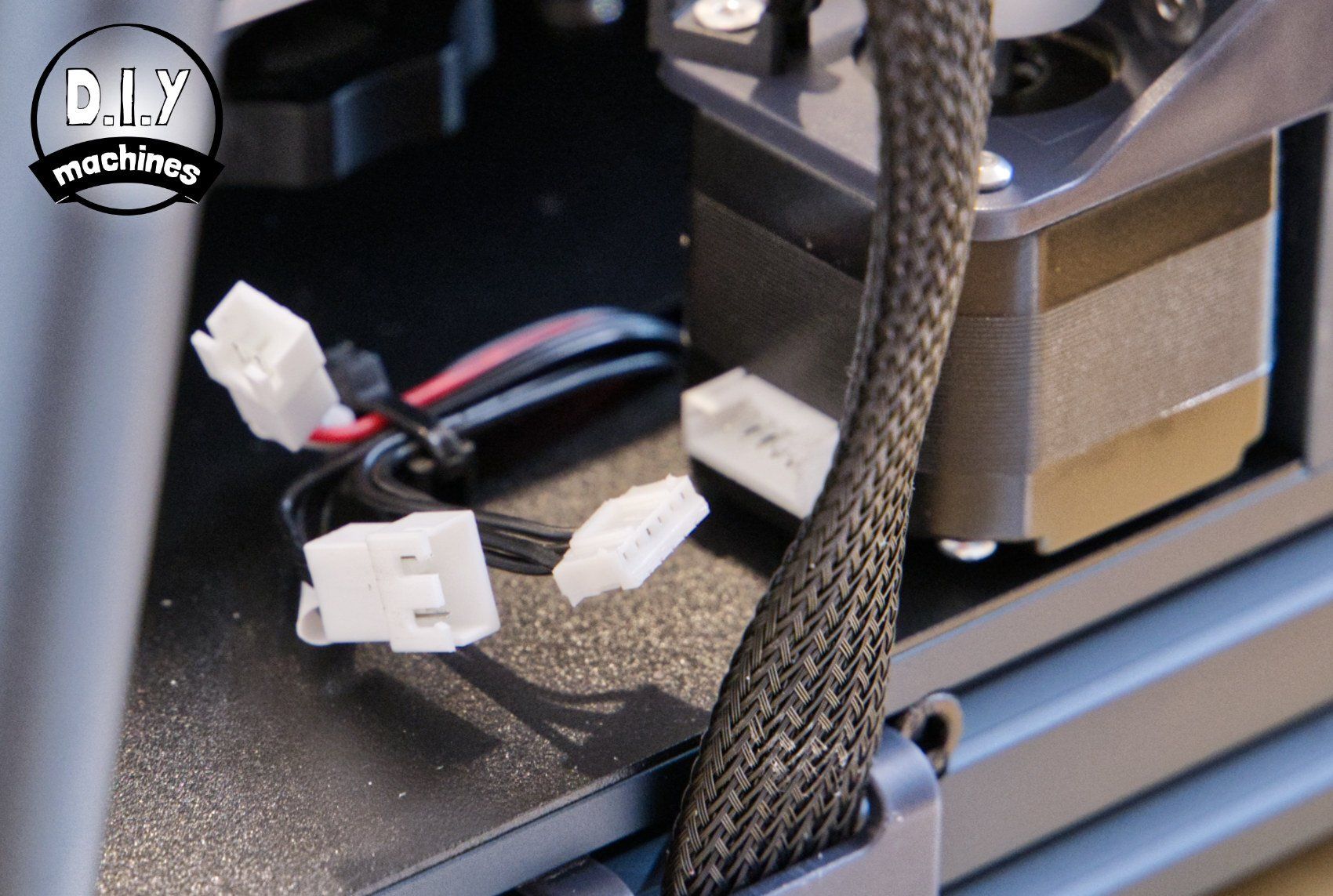
Well, I say impossible, but I did make an honest mistake. The large collection of neatly bundled wires from the bed first stop at the X axis motor (on the left hand side of the vertical gantry) before carrying on to the print head itself where they terminate. As the machine is shipped with the X axis at the top of the gantry I, without thought or warning from the instructions, passed the wire behind the brace and into the print head.
This is not a problem towards the top of the machine, however, as the X axis lowers when calibrating the printer for the first time, the support rod which I had passed the wiring loom around becomes further from the gantry. Ultimately, as the print head reached the printing bed the path the wiring was now taking from the X-axis motor to the print head was great then the length of the cable and itself so it begun to pull away from the connector before I killed the power.
Nothing was damaged and I simply had to reroute this one cable to between the support rod and vertical extrusion of the printer. A re-visit of the manual shows that (most likely for clarity) the cable paths themselves are not included in the drawings. I feel that this one possibly common mistake warrants an additional step to clarify its correct path in the instructions.
Instruction manual
Talking of instructions, the instructions are concise and mostly in a pictorial form. I had no problem consulting them except for the missing warning about routing the print head cable. Take a look at the manual yourself if you would like - I have linked to it for your personal perusal.
Elegoo have also included a handy video guide of the assembly procedure which you will find saved on the memory stick included with your new printer. Thanks Elegoo. 😊
First Print
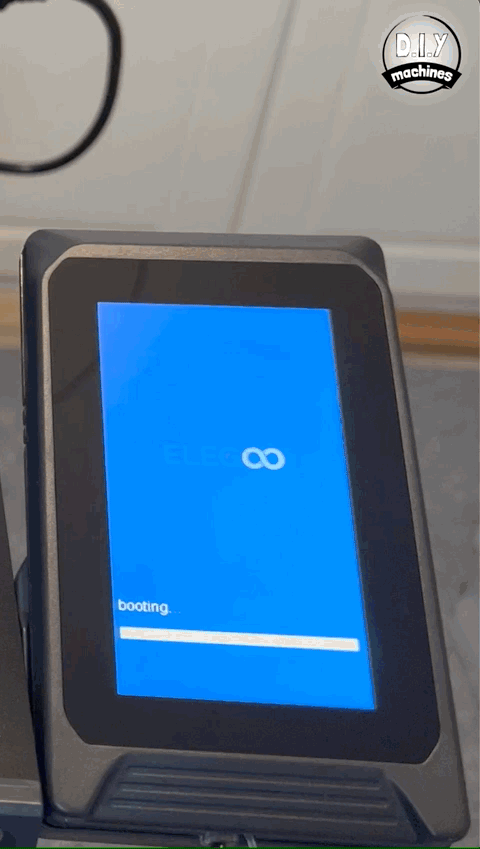
Levelling the Bed
The printer automatically measures the height of the print surface across a grid of 49 unique points and uses this information to calculate a mathematical model it refers to whilst printing to compensate for any warping of the print bed.
Once this automatic routine has completed you need only to set the layer height of the first layer. This simply requires you to continuously slide a piece of common paper back and fourth under the nozzle whilst lowering it with the touchscreen until you feel some slight resistance.
This process was incredibly easy and proved accurate as no further tweaks were required when making the proceeding test prints.
The instructions for levelling the print bed have improved greatly since the Neptune 3 Pro - something I called to attention when reviewing the Pro iteration. It shows Elegoo listen and act upon feedback to ensure their development inches closer towards both a fantastic printer and set-up experience.
Loading the Filament
This a process improved on both the Pro and Plus machines. It has become a simple case of passing the filament effortlessly though the detector at the top of the gantry, pressing the comfortable lever on the top of the print head before inserting the filament a few cm's and then releasing.
All that is left to do is to heat the nozzle using the touchscreen (Elegoo provides a handy set of presets for common materials) and pressing load. Done.
Printing the included Sample Model
I always start by printing any bundled models using any bundled filament for the printers first print. It seems fair to use it in its best light.
The Buddha is their chosen test print and I can gladly say that I can't see any glaring issues with the print quality. No surprise their of course. However, printing a model Elegoo have pre-selected and using their supplied filament does not provide ample opportunity to stress the machine. And in this case it certainly doesn't demonstrate the printers ability to create large items!
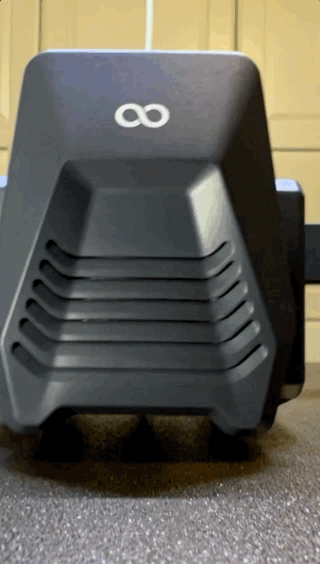
Click on either of the photos of the sample print to view a larger size and judge the quality for yourself. I am very impressed. It was printed at a 0.15mm layer height. No lifting or warping of the base occurred and extrusion appears to be consistent.
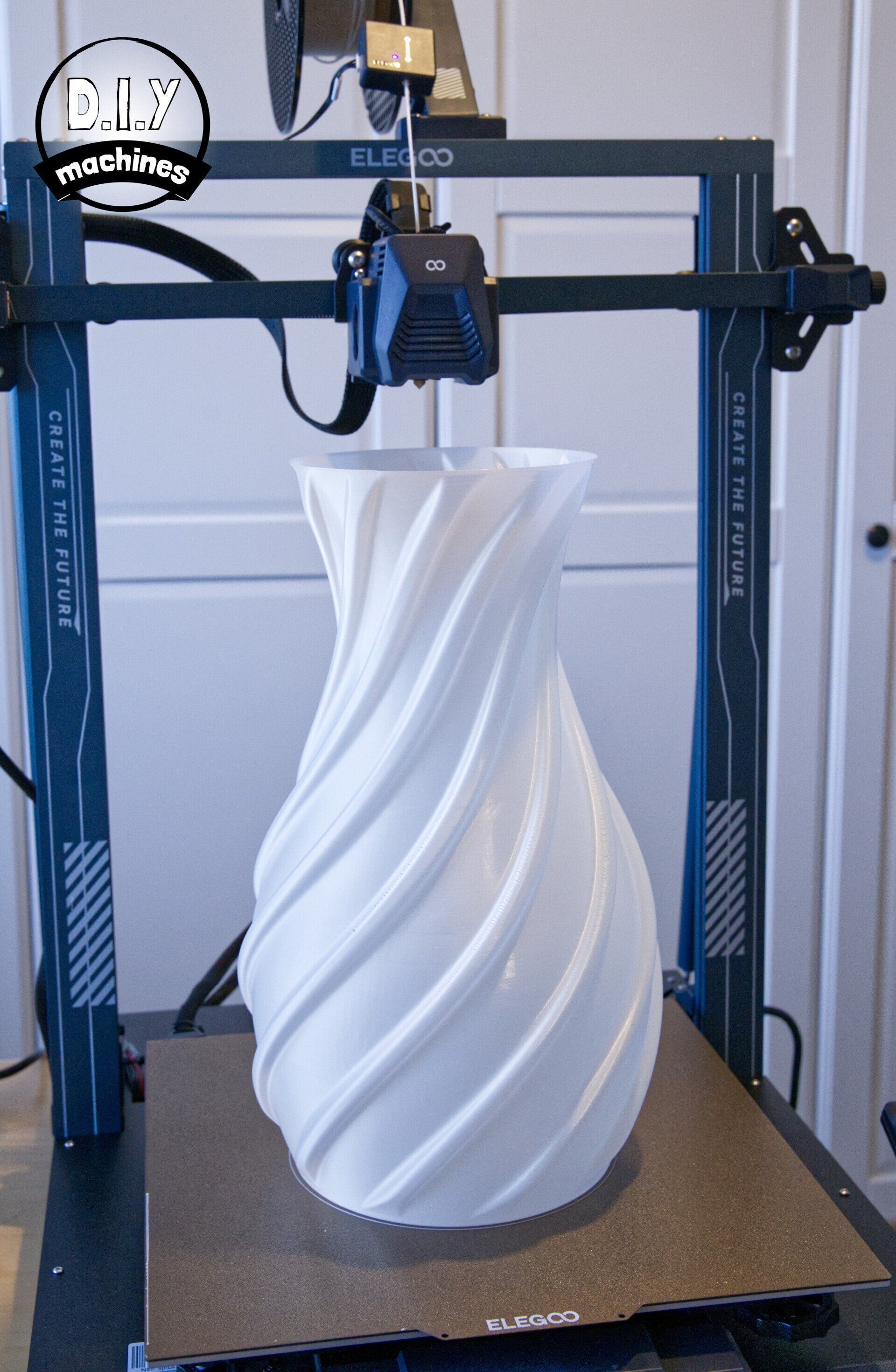
Printing gets bigger
This the largest object I have ever printed on a 3D printer myself. It's a vase design I found on Printables which was naturally printed using 'Vase Mode'.
It measures 21.8cm in width and 36cm in height - it printed first time without hiccups. After the print bed had cooled it was removable from the print bed with the gentlest of touch.
Total time to print was around 10.5 hours and I used PLA.
This has me rather excited. It is mildly frustrating when the size of your build plate limits your options for designing and printing items. As much as I am unlikely to use the full print volume for a single item in my public projects (I need to ensure others can print the parts on smaller printers) it does allow me to print several parts overnight or build larger items for personal projects.
I have a roll of two tone filament which I can't wait to print an additional vase design with. And this ability to print vases in a larger size seems to lend the vase a feeling of luxuriousness.
The image can be clicked on and enlarged to allow for much closer inspection should you wish.
Torture Test
This print is designed to stress the machine a little more.
I will print the same one created by AutoDesk and Kickstarter I use on all FDM printers which I review. This allows us to push the limits of the machine such as overhang, bridging, and retraction abilities. It also allows for a fair and convenient comparison.
I have used PrusaSlicer 2.5.0 to prepare the G-code.
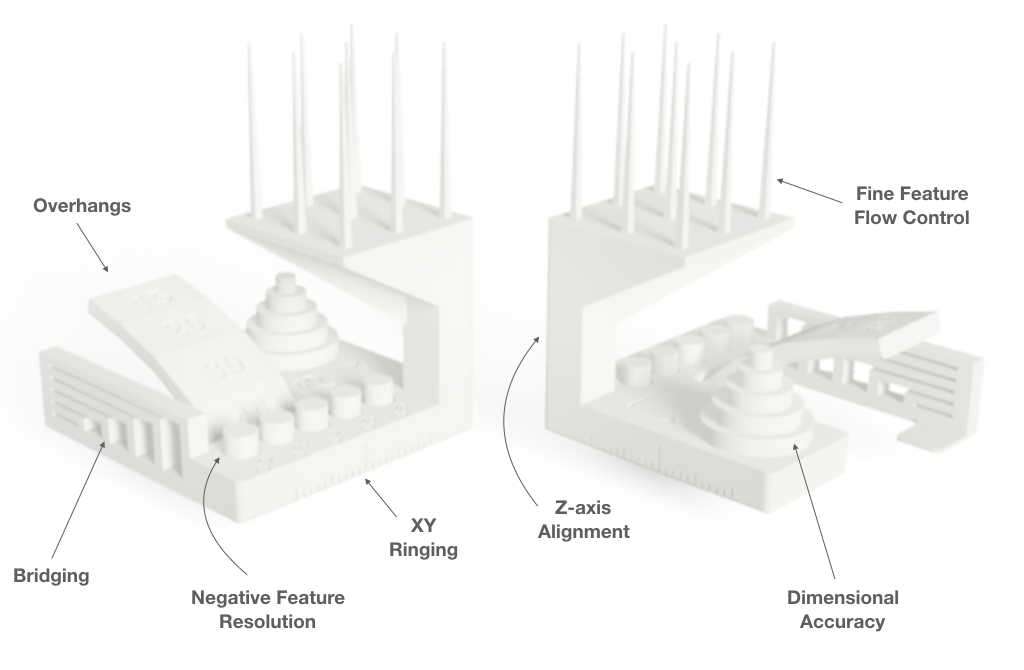
Don't forget to click on any image to open a higher resolution copy to inspect for yourself.
I am impressed with the quality for the price point. There is evidence of slightly more stringing on the points at the top in comparison to the Neptune 3 Pro though it is certainly no issue. A quick wave of a heat gun entirely removes the strings as they're so fine. All five of the Negative Feature test items came out without any issues. The bridging tests are fine and the overhang only shows signs of struggling at 45º, though it still did achieve it. The two internal perimeters of the Fine Feature test platform are hanging away from the other strands. I can't be certain if this is an issue of the printer or slicing software - it doesn't constitute a failure but it's not desirable either.
Software
Elegoo have customised a copy of Cura to be used as a Slicer for preparing your prints to be printed. If you're not familiar with Slicing Software then it's the middle stage which takes your computerised 3D models and 'Slices' it into individual layers, usually 0.15mm or 0.2mm in height. Each one of these layers is then prepared as a series of paths for the printer to follow before it raises its print head for the next layer.
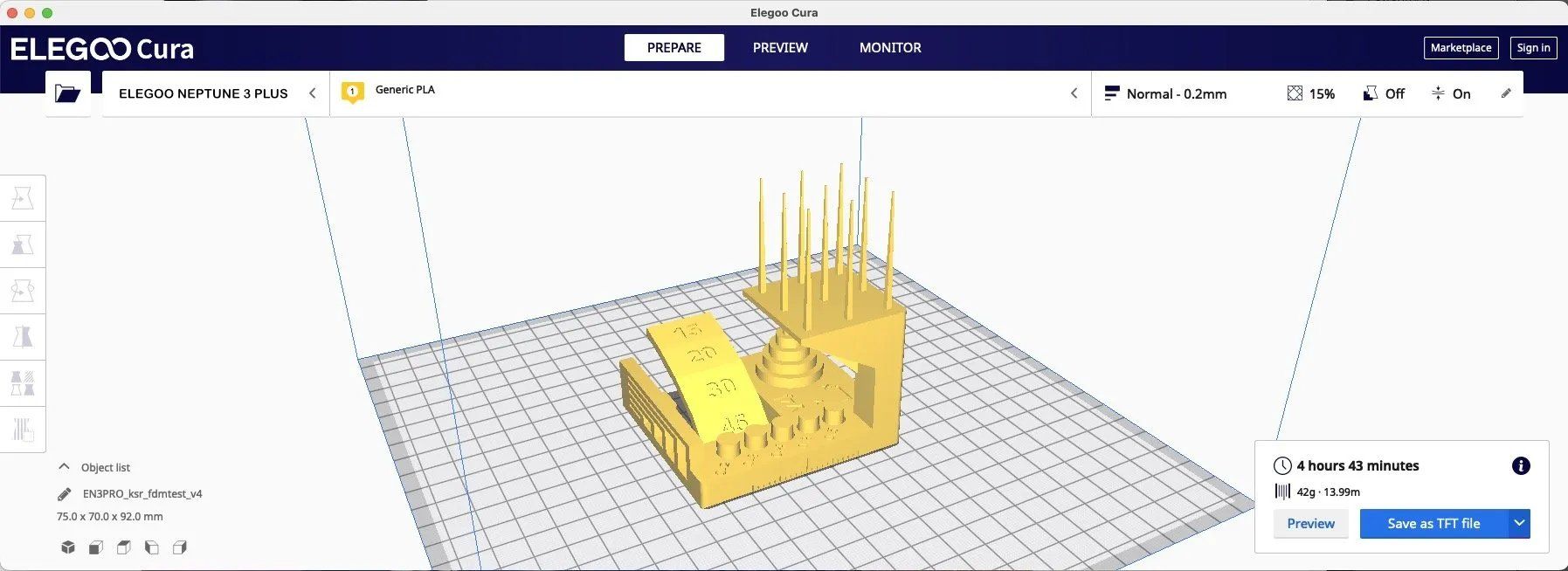
The software can have as much an impact on print quality as the hardware itself. They go hand in hand. For example it's the Slicers responsibility to calculate support structures if required and deal with the acceleration and deceleration of the print head in order to balance the need for a desirable print speed without introducing print artefacts into the finished model.
The version of customised Cura included on the memory card of my test machine was 4.8. Cura is currently on version 5.2.1 and as such it prompted me to update. I obliged only to realise that the latest version of Cura did not contain the printer profiles for many of Elegoos latest printers including the Neptune 3 Pro or Plus. Perhaps they will include it in the future, but for now it means we cannot take advantage of the advancements in Slicing Software past version 4.8.
Final Thoughts
I would not hesitate to recommend this printer to someone looking for a large format printer from a recognised brand at a sensible price.
The print size increase is going to be very welcome. With my current machine I often set an alarm to wake me up through the night so that I can remove a finished print and start the next. On the Elegoo Neptune Plus I will be able to add several models to the print bed and enjoy a good nights sleep!
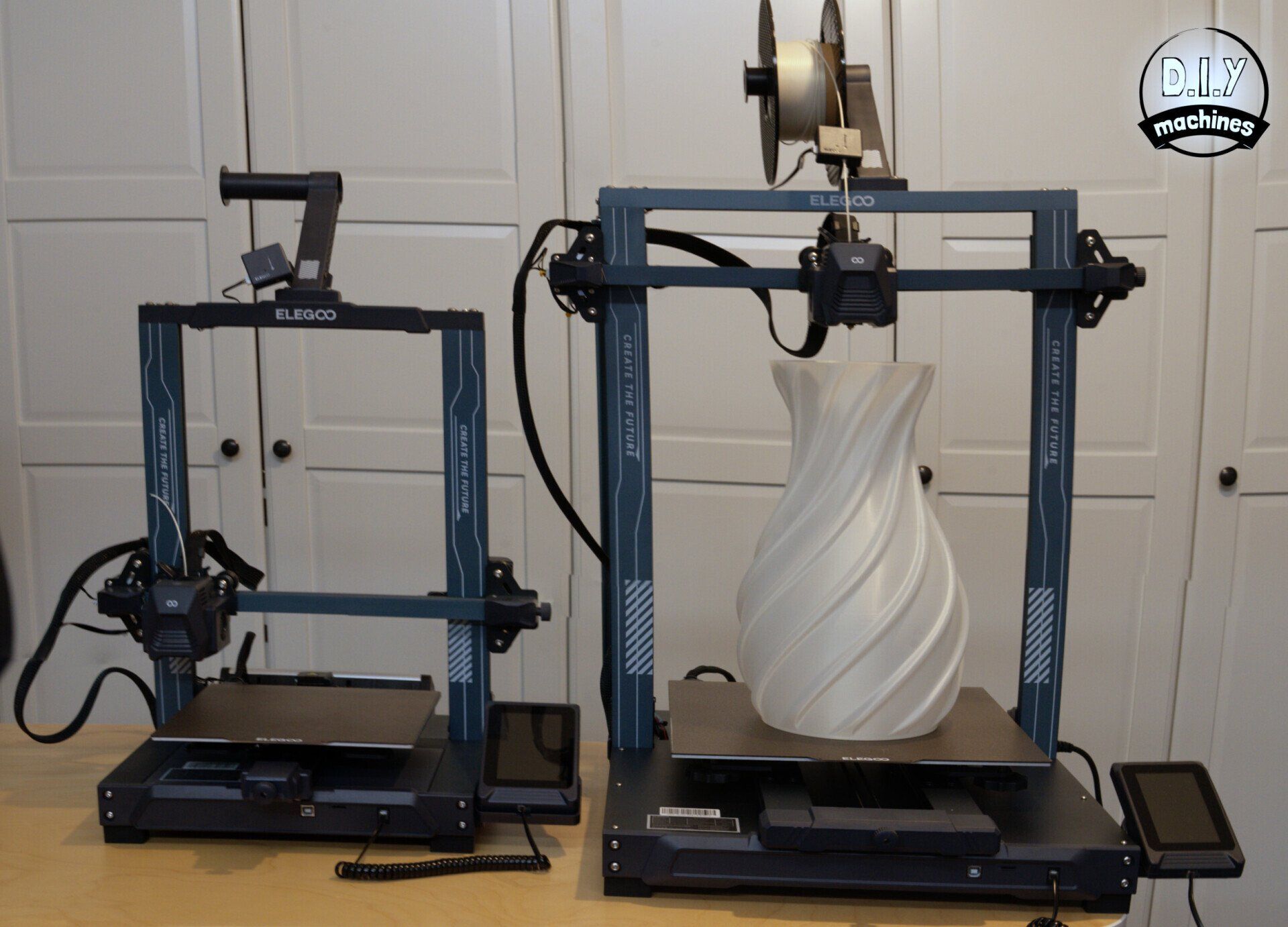
The machine itself looks smart. And as for Elegoo themselves, I recently had a problem with a resin printer of theirs and their support representatives where extremely helpful and promptly solved my problem (they sent a new motherboard and some resin for the inconvenience) so I have no issues with the brand.